Mold making
High precision moulds for complex geometries
The MPT Plastics mechanical workshop works in a continuous cycle, creating optimized moulds that meet the quality standards for any product sector, thanks to a detailed design and the use of cutting-edge technologies.
Reduction of product defects.
Resistance to the productive stress of stamping.
High productivity that persists over time.
MPT’s “Design and Development” office assists the customer in designing moulds for any application sector, including those commonly referred to as “difficult-to-cut” that is difficult to work with traditional techniques because of their high mechanical characteristics. Precision instruments are in our DNA, in fact it was 1978 when the first die-sinking EDM machinery entered our mold-making workshop.
One optimized, the digital models generated by our team of designers and engineers, are transferred to the department “Production” equipped with a mechanical workshop equipped with the latest technology and equipment. Each mould, new or repaired, is carefully tested inside before delivery. The synergy between the mold production workshop ant the moulding department allows us to ensure the constant improvement of the processes and the qualitative performance of the final products.
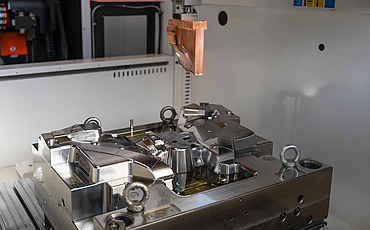
The stages of mold making in MPT
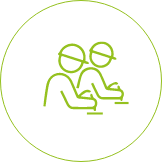
Technical Design and Codesign
Early on, our highly skilled engineers use advanced computer-aided design (CAD) software to create a detailed mold design. The design considers not only the external shape of the finished product but also the internal optimization of the equipment. This includes the strategic arrangement of cooling channels, gate position (plastic entry points), and other features to ensure precise temperature control during the molding process.
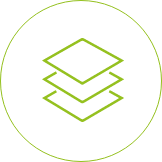
Selection of Materials and Manufacturing Processes
MPT engineers choose the highest quality materials, such as special wear and heat resistant steels. These materials are machined with the latest generation CNC machines, which offer unmatched dimensional accuracy.
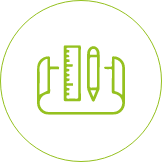
Use of Advance Technologies
The MPT mold making workshop is equipped with high precision machine tools, such as numerical control machines (CNC) and numerical control EDM. They ensure high dimensional accuracy and allow you to create extremely precise details in the mold. This technology is critical for creating intricate and complex features within the mold. In addition, the use of high-speed milling machines (HSM) ensures a flawless surface finish, minimizing the need for additional finishing machining.
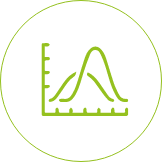
Quality Control and Optimization
During and after the manufacturing process, the mould undergoes extremely strict quality control. Advanced measuring instruments, such as coordinate measuring machines (CMM), are used to verify compliance with dimensional specifications. Any deviation is immediately corrected through small changes and optimizations. After the construction molding machine and tested to ensure it works properly and produces parts that meet specifications.
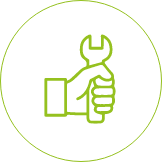
Prevetnive Maintenance and Continuous Improvements
After installing the mold on the injection moulding machine, our workshop implements preventive maintenance programs to ensure optimal performance over time. This includes cleaning, lubrification and inspection to detect any signs of wear or damage. In addition to the manufacture of moulds from scratch, the MPT mechanical workshop also provides service and maintenance of existing mould entrusted to specialized workers who carry out manual overhauls and refinements.
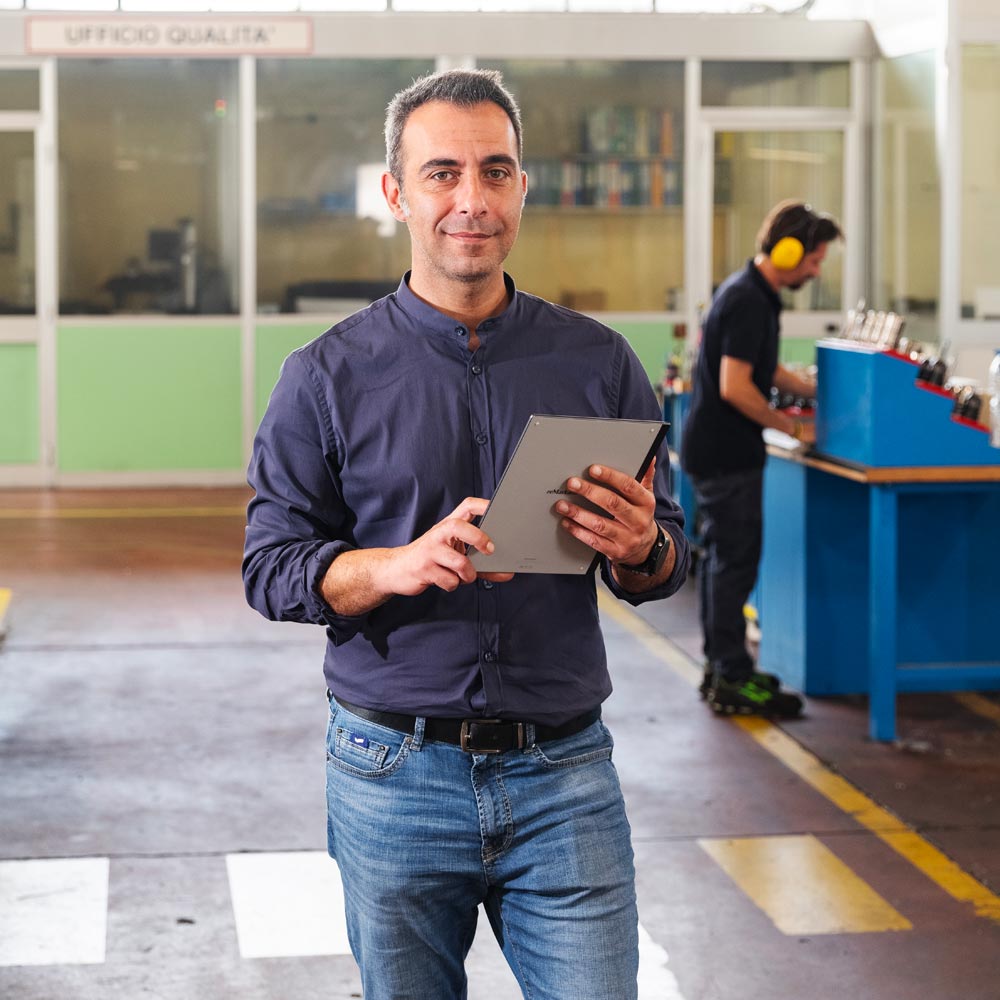
"Not only state-of-the-art equipment but also a team of highly qualified professionals who work in synergy during all phases. This integrated approach to manufacturing high precision molds is crucial in such an advanced and competitive market."
Gabriele Rossi
Responsabile Officina Stampi